烧毛机与预缩联动储送组合装置技改研究
1.项目的提出
牛仔布后整理工序的设备原设计是烧毛、上浆、拉幅、拉斜、烘燥联成一组(简称烧毛机组,见图1—a),喷水加湿、预缩、烘燥为一组(简称预缩机组,见图1—b)分开运行的。随着工艺、质量和生产管理要求的不断深化,逐步暴露出两个突出的问题:
(一)布面产生摺痕疵点:坯布经烧毛机组的烧毛、上浆、拉斜、烘燥后经由摆斗摺叠存放在运输车上,每车存放800米左右,重560公斤左右。由于上浆、烘燥后布面较硬、温度很高,在运输车上堆积的布自身布重的压力很大,因此形成了自然的热定型条件,使摺叠的布在预缩机处理后,出现明显的摺痕,造成布面一条条色泽较深的疵点,严重影响了布面的外观。以93年5月份为例,摺痕疵分占总后整理疵分的80.7%。
(二)重复劳动:由于连续生产的需要,烧毛之前须将经初验后存放在运输车上的布,头尾连接起来,但因为烧毛机组与预缩机组是分开单独运行的,所以烧毛、拉斜处理后的布,须再存放在运输车上并把原来缝接头撕开,推到前方20远的预缩机组处,再将运输车上的布头尾缝接起来,成为:缝接—撕开—再缝接的重复劳动过程。
2.设计的要点及实施
如果能实现两机组联动,则烧毛、拉斜处理出来的布就不需要放在运输车上,而直接进入预缩机组,这样上述两个问题就可以迎刃而解了。为此,本人在对引进后整理设备做好消化、吸收的基础上,围绕两机组联动的有关问题,设计并主持进行了以下的研究改进,于93年五月底完成技改工作,取得了显著的效果:
(一)实现两机组联动首先要解决布面的朝向
正常情况下,烧毛机组烧毛、拉斜处理时进布是布面朝上的,而预缩机组预缩的进布是布底朝上的。预缩机由于工艺要求布面不可接触烘筒,进布时必须使布面朝下,因此要实现两机组对接联动就必须解决由烧毛时进布布面朝上转为进入预缩机处理时进布布底朝上的问题。
由于烧毛的工艺要求必须烧布面,如图1—a,如果进布布底朝上则喷火嘴就烧不了布面了,必须把喷火嘴装到图1—a中的c、d位置,这样改动量很大。如果按图1—b那样;底朝上进布,改变烧毛室的绕法,则喷火嘴仍可烧布面,但这样烧毛室出布要从上面引出,是否会挡住烧毛时污气的排出?经试验证明污气并无外溢。这是由于排气系统吸力较大,污气从布的横向向两侧排出了。这样只要改变烧毛室的绕法,后整理过程中布面转向的问题就解决了。
(二)联动装置设计的实施
烧毛机组与预缩机组两机组都很长,而且两机组之间相距有20米之远。两机组相连的条件是:1、两机组的速度要同步(这一点由于两机组都是直流电机传动,容易做到)。2、中间应有不少于300米的储布量,以便处理如下情况:①值车工发现速度不同步时调正;两机组中一机组有小故障时,临时停车几分钟,另一机组可继续运转;③两机组中一机组须紧急停车,另一机组来提及配合停车。
如果联动装置能采用一个斜面的架子,让烧毛机组处理后送布辊送出来的布成鱼鳞状地落在斜面上,依靠布匹自重缓缓滑下送至后方的预缩机组,有一定的储量后,再开动预缩机组拖动布匹进行预缩,这是比较理想的简易方法(它可省去一套复杂的传动运输装置),问题的关键是如何选择架子合适的斜面坡度及确定烧毛机组送布辊的合适高度。为此,进行了两项工作:1、应用力学原理对不同布重计算设计不同的坡度,并在生产现场进行不同坡度的落布模拟试验,最后确定以正切角12°为最佳坡度,此时落布缓缓下滑,分布均匀;2、观察分析烧毛机组送布辊的落布情况,要求送布辊送出的布必须有一个抛物形的落差动力,使布送出时远离送布辊既不会发生反卷现象又可推动前方的存布下滑,确定将送布辊往前移约一米和向上提高一米,并在斜坡上部安放一块成抛物线形的不锈钢板,经试验情况良好,在到预定的要求。
(三)改造前后的情况见可以看出,烧毛机组处理出来的布不必装在储布运输车上,而是缓缓地从装置的斜面均匀地滑下,送至预缩机组前,直接进入预缩机组预缩,从而消除形成摺痕的条件,解决了摺痕这一疵点。
3、烧毛机组与预缩机组之间的联动装置自投入使用以来,无论是布匹的缓缓下滑、中间的储布量,还是两机联动的生产配合,都达到了预期联动和储送的效果。由于避免了储布运输车产生的摺痕,提高了产品质量,产品入库一等品率提高了2.7%,同时减少了用工和储布运输车辆的制造及维修费用,一年就可为企业增加21.032万元的经济效益。根据行家评议,对后整理工序烧毛机组与预缩机组的联动装置的设计,将原烧毛机组和预缩机组分开运行的生产方式改为联动,形成流水线生产,技术先进,经济合理,结合生产实际,开创了国内同类机型的先例,达到了国内先进技术水平,得到了美国莫里森纺织机械公司技术专家的肯定。
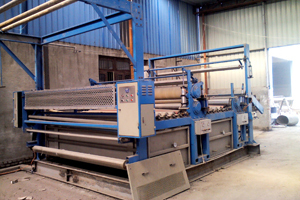
|